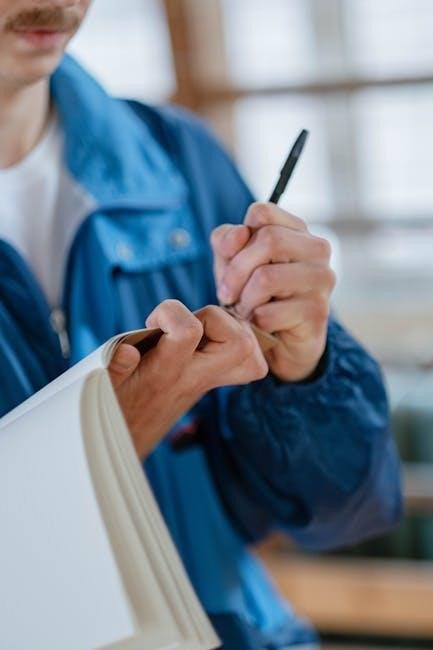
Manual handling training is essential for reducing workplace injuries by teaching safe lifting and handling techniques. Trainers play a crucial role in educating employees to prevent musculoskeletal disorders and ensure compliance with health and safety regulations, fostering a safer work environment.
1.1 Overview of Manual Handling Training
Manual handling training focuses on teaching employees safe techniques to lift, carry, and move objects, reducing the risk of injury and promoting a safer workplace. It covers proper lifting postures, load assessment, and the use of equipment to minimize strain. The training emphasizes practical exercises and real-life scenarios to ensure competency. Employers are responsible for providing this training, which is often delivered by certified trainers. The goal is to create awareness and equip workers with the skills to handle tasks safely, aligning with health and safety regulations and reducing workplace accidents effectively.
1.2 Importance of Training the Trainer
Training the trainer is vital to ensure manual handling instructors possess the necessary knowledge and skills to effectively teach others. It ensures consistency in training delivery, compliance with legal standards, and enhances the trainer’s ability to address workplace-specific risks. Trained trainers can adapt to diverse learning needs, fostering a culture of safety and reducing workplace injuries. This empowerment directly impacts employee well-being and organizational productivity, making it a cornerstone of effective health and safety management.
1.3 Target Audience for the Training
The target audience for manual handling training includes employees involved in manual handling tasks, new hires, and those changing roles requiring physical labor. Supervisors and safety officers also benefit to ensure compliance and effective oversight. The training is tailored to address the specific needs of each group, ensuring they understand safe practices and legal requirements. This targeted approach helps create a safer workplace, reduces injury risks, and promotes a culture of health and safety compliance across all levels of the organization.
Understanding Manual Handling
Manual handling involves the movement of objects by hand, a common task in many industries; Understanding its principles is crucial for preventing injuries and ensuring workplace safety effectively.
2.1 Definition and Scope of Manual Handling
Manual handling refers to the movement or support of loads by hand or using bodily force. It encompasses lifting, lowering, pushing, pulling, carrying, or holding objects. The scope includes various industries, such as healthcare, manufacturing, and logistics, where physical tasks are common. Understanding this definition helps identify risks and implement safety measures, ensuring compliance with regulations and reducing workplace injuries. Effective training focuses on proper techniques and equipment use to minimize strain and enhance overall safety. This foundational knowledge is vital for trainers to convey to employees.
2.2 Key Principles of Safe Manual Handling
The key principles of safe manual handling emphasize assessing the load, adopting proper posture, and using efficient techniques to minimize strain. Maintaining control throughout the task, avoiding twisting, and keeping loads close to the body are crucial; Additionally, using mechanical aids when possible and ensuring a stable working environment further reduce risks. Trainers should focus on these principles to equip employees with the knowledge and skills needed to handle tasks safely and effectively, preventing injuries and promoting workplace well-being.
2;3 Common Manual Handling Injuries and Risks
Manual handling injuries often include musculoskeletal disorders, back injuries, sprains, and strains. These typically result from repetitive tasks, poor lifting techniques, or handling heavy loads. Awkward postures and insufficient recovery time exacerbate risks. Employees in roles requiring frequent lifting or bending are particularly vulnerable. Such injuries can lead to absenteeism, reduced productivity, and increased healthcare costs. Understanding these risks is critical for trainers to emphasize preventive measures and promote a safer working environment, ultimately benefiting both employees and employers by reducing injury-related disruptions.
Legal and Regulatory Requirements
Employers must adhere to health and safety laws, including the Manual Handling Operations Regulations 1992, ensuring safe practices and providing proper training to prevent injuries and legal liabilities.
3.1 Employer Responsibilities in Manual Handling
Employers are legally required to assess manual handling risks, provide appropriate training, and implement control measures to minimize injuries. They must ensure employees understand safe techniques and report concerns. Regular monitoring and updates to safety protocols are essential to maintain compliance with regulations and protect workers’ health.
3.2 Employee Rights and Obligations
Employees have the right to a safe working environment and training on manual handling. They must follow safety procedures, use provided equipment, and report hazards or injuries. Obligations include cooperating with employers to reduce risks, attending training sessions, and adhering to safe practices. Understanding these rights and duties ensures a safer workplace and legal compliance.
3.3 Relevant Health and Safety Regulations
Manual handling is governed by specific health and safety regulations, such as the UK’s Manual Handling Operations Regulations 1992. Employers must assess risks, provide training, and implement controls. Employees’ rights are protected under these laws, ensuring safe working conditions. Non-compliance can lead to legal penalties. These regulations aim to reduce injuries and promote a safe work environment by establishing clear guidelines for manual handling practices.
Risk Assessment in Manual Handling
Risk assessment is crucial in manual handling to identify hazards and implement safety measures. Evaluating tasks helps reduce injuries and ensures compliance with safety standards.
4.1 Steps to Conduct a Manual Handling Risk Assessment
Conducting a manual handling risk assessment involves identifying tasks, evaluating the load, environment, and individual factors. Observing employees and consulting with them helps pinpoint hazards. Next, assess the risk level using tools like the Manual Handling Assessment Chart (MAC). Implement control measures such as ergonomic adjustments or equipment use. Monitor and review the assessment regularly to ensure ongoing safety. Training employees and ensuring compliance with regulations are also critical steps in this process to minimize injury risks effectively.
4.2 Identifying High-Risk Tasks
High-risk manual handling tasks often involve heavy loads, awkward postures, or repetitive movements. These tasks are identified through observations, employee feedback, and risk assessment tools like the Manual Handling Assessment Chart (MAC). Tasks requiring excessive force, bending, or twisting are prioritized for intervention. By pinpointing these high-risk tasks, trainers can focus on implementing targeted control measures to reduce injury risks and improve workplace safety. Early identification ensures proactive strategies to mitigate hazards effectively;
4.3 Implementing Control Measures
Implementing control measures is essential for reducing manual handling risks. Engineering controls include mechanical aids like hoists or ergonomic workstations. Administrative controls involve task rotation and safe lifting policies. Personal Protective Equipment, such as gloves and back supports, also plays a role. Trainers should ensure these measures are understood and applied consistently, with ongoing monitoring and feedback to assess effectiveness and make necessary adjustments for a safer and healthier workplace environment.
The Role of the Trainer
Trainers must possess adequate qualifications and communication skills to deliver effective manual handling training, ensuring a safe and engaging learning environment for all participants.
5.1 Qualifications and Competencies Required
Trainers must hold relevant certifications in health and safety, with expertise in manual handling. They should demonstrate strong communication and instructional skills, ensuring engaging and effective training delivery. Practical experience in manual handling is essential, along with knowledge of legal and regulatory standards. Trainers must also stay updated with industry best practices to provide accurate and comprehensive guidance, ensuring trainees develop the necessary skills to perform tasks safely and efficiently in the workplace.
5.2 Effective Communication Strategies
Effective communication involves clear, concise instruction and active engagement with trainees. Trainers should use demonstrations, visual aids, and real-life examples to enhance understanding. Encouraging questions and discussions fosters a collaborative learning environment. Providing feedback and using varied teaching methods ensures that all learning styles are addressed, promoting better retention of manual handling techniques and safety practices. Trainers must adapt their communication style to meet the needs of diverse trainee groups, ensuring that everyone grasps the essential skills and knowledge effectively.
5.3 Creating an Engaging Learning Environment
Creating an engaging learning environment for manual handling training involves interactive and hands-on approaches to keep trainees interested and promote effective learning. Incorporating real-life examples, group activities, and discussions can enhance understanding and retention. Using visual aids like videos to demonstrate correct and incorrect techniques can make the training more relatable. Providing immediate feedback during practice sessions allows trainees to correct mistakes promptly. Tailoring the content to specific job roles and incorporating positive reinforcement can increase engagement. Combining clear instruction with interactive activities ensures a practical and memorable learning experience.
Manual Handling Techniques
Manual handling techniques focus on safe lifting, carrying, and lowering methods to minimize injury risks. Proper posture, balance, and use of equipment are emphasized to enhance workplace safety.
6.1 Proper Lifting Techniques
Proper lifting techniques are fundamental in manual handling to prevent injuries. Trainees should bend at the knees, keep the load close to the body, and lift using leg muscles instead of the back. Maintaining a neutral spine and avoiding twisting movements are crucial. Demonstrating these techniques ensures trainees understand how to safely lift and lower objects, reducing the risk of musculoskeletal disorders. Practical exercises and real-life scenarios help reinforce these methods, promoting a safer working environment.
6.2 Safe Carrying and Lowering Methods
Safe carrying involves maintaining good posture, keeping the load close to the body, and avoiding uneven weight distribution. When lowering, bend at the knees and hips to minimize back strain. Ensure the load is placed gently on a stable surface, avoiding twisting movements. Trainees should plan their path beforehand to prevent obstacles. Proper grip and balance are essential during transport, and using assistive equipment can reduce strain. Emphasizing these techniques helps trainees master safe carrying and lowering practices, reducing injury risks and improving workplace safety.
6.3 Use of Equipment and Aids
The use of equipment and aids, such as trolleys, hoists, and slings, can significantly reduce physical strain during manual handling tasks. Trainers should emphasize proper usage techniques to ensure safety and efficiency. Demonstrating how to select the right tool for the task is crucial, as well as explaining how to maintain and inspect equipment regularly; By incorporating equipment and aids into training, trainers can help minimize manual handling risks and promote a safer working environment for all employees.
Training Delivery Methods
Effective manual handling training can be delivered through classroom sessions, on-the-job practice, or e-learning modules. Each method ensures comprehensive coverage of safe techniques and practical application.
7.1 Classroom-Based Training
Classroom-based training provides a structured learning environment for manual handling, allowing trainers to deliver comprehensive instruction. It incorporates group activities, live demonstrations, and interactive sessions. This method ensures trainees receive consistent information and can ask questions in real-time. Hands-on practice within a controlled setting helps reinforce proper techniques. Trainers can immediately address misunderstandings, enhancing overall understanding and compliance with safety standards. This traditional approach remains effective for fostering engagement and practical skill development among participants.
7.2 On-the-Job Training
On-the-job training allows trainees to apply manual handling skills directly in their workplace. This practical approach enables employees to learn by performing actual tasks under supervision. Trainers provide immediate feedback, ensuring proper techniques are used to minimize injury risks. Real-life scenarios enhance understanding and relevance, making the training more engaging. OJT complements classroom instruction by reinforcing safe practices in a familiar environment, ensuring trainees are proficient in their specific job requirements and workplace conditions.
7.3 E-Learning and Online Modules
E-Learning and online modules offer flexible and accessible manual handling training. These platforms allow employees to complete courses at their own pace, ensuring convenience and consistency. Interactive content, such as quizzes and videos, engages learners and reinforces safety practices. Online modules also provide tracking features, enabling employers to monitor progress and ensure compliance with training requirements. This method is particularly effective for remote workers or those with conflicting schedules, making it a valuable addition to traditional training methods.
Practical Exercises and Demonstrations
Practical exercises and demonstrations bridge theory with real-world application, enabling trainees to practice safe manual handling techniques in a controlled environment, enhancing their competence and confidence.
8.1 Hands-On Practice Sessions
Hands-on practice sessions are crucial for developing practical skills in manual handling. Trainees engage in real-life scenarios, applying techniques learned in a controlled environment. These sessions focus on proper lifting, carrying, and lowering methods, allowing individuals to build muscle memory and confidence; Trainers provide immediate feedback, correcting poor practices and reinforcing safe habits. Group activities encourage teamwork and problem-solving, ensuring trainees can handle diverse tasks effectively. This experiential learning reduces injury risks and enhances overall competence in manual handling procedures.
8.2 Real-Life Scenarios and Case Studies
Real-life scenarios and case studies are invaluable for manual handling training. They provide practical examples of common hazards and solutions, helping trainees understand how to apply safe practices in real-world situations. By analyzing specific incidents, trainees can identify risks and learn how to implement effective control measures. Group discussions on case studies encourage active participation, fostering a deeper understanding of manual handling challenges and promoting the sharing of best practices to enhance workplace safety and reduce injury risks.
8.3 Group Activities and Discussions
Group activities and discussions are key components of effective manual handling training. They encourage active participation, fostering collaboration and shared learning among trainees. Interactive exercises, such as role-playing or problem-solving tasks, help trainees apply theoretical knowledge in practical scenarios. Group discussions also allow trainees to share experiences and perspectives, enhancing their understanding of manual handling challenges. These activities promote engagement, improve retention of safety practices, and equip trainees with the confidence to handle real-life situations effectively, reducing workplace injuries and improving overall safety standards.
Monitoring and Feedback
Monitoring trainees during practical sessions ensures they apply safe manual handling techniques. Constructive feedback reinforces correct practices and identifies areas for improvement, enhancing overall safety standards.
9.1 Assessing Trainee Competency
Assessing trainee competency ensures they can safely perform manual handling tasks. Practical demonstrations, quizzes, and real-life scenario evaluations are effective methods. Trainers observe adherence to safety guidelines, proper lifting techniques, and overall understanding. Feedback is provided to address gaps and reinforce correct practices, ensuring trainees meet required standards before certification. This step is crucial for maintaining workplace safety and reducing injury risks.
9.2 Providing Constructive Feedback
Providing constructive feedback is essential for improving trainees’ manual handling skills. Trainers should focus on specific actions, using clear examples and suggesting practical improvements. Feedback should be delivered respectfully, emphasizing strengths and areas for growth. Timely and actionable comments help trainees understand and correct their techniques. This approach fosters a supportive learning environment, encouraging trainees to ask questions and refine their practices, ultimately enhancing overall competency and workplace safety.
9.3 Continuous Improvement Strategies
Continuous improvement strategies are vital for refining manual handling training programs; Trainers should regularly gather feedback from trainees to identify areas for enhancement. Implementing new techniques, tools, and technologies can keep training engaging and effective. Additionally, staying updated with industry trends and regulatory changes ensures the content remains relevant. By fostering a culture of ongoing development, trainers can consistently deliver high-quality training, reducing workplace risks and improving overall safety standards; This proactive approach ensures the program evolves to meet the needs of both employees and the organization.
Certification and Accreditation
Certification and accreditation ensure trainers meet professional standards, validating their expertise in manual handling. Accredited programs guarantee high-quality training, fostering compliance with safety regulations and enhancing workplace safety.
10.1 Types of Certifications Available
Various certifications are available for manual handling trainers, including accredited programs by recognized bodies such as City & Guilds. These certifications validate expertise in delivering safe manual handling techniques, ensuring compliance with legal standards. They often cover risk assessment, practical demonstrations, and training delivery methods. Online and classroom-based certifications are also offered, providing flexible learning options. These credentials enhance a trainer’s credibility and ensure they are equipped to effectively train employees in safe manual handling practices, reducing workplace injuries and promoting a safer environment.
10.2 Accreditation Process for Trainers
The accreditation process for manual handling trainers typically involves completing a recognized training program, such as those offered by City & Guilds. Trainers must demonstrate competence in delivering manual handling training, including risk assessments and practical techniques. Many programs require passing an exam or assessment to ensure proficiency. Accreditation often involves continuous professional development to maintain certification. Trainers must also stay updated on legal and regulatory changes to provide accurate and compliant training. Accreditation ensures trainers are qualified to effectively teach safe manual handling practices, reducing workplace injuries and promoting a safer work environment.
10.3 Renewal and Updating Certifications
Certifications for manual handling trainers typically require renewal to remain valid. This process often involves completing continuing professional development (CPD) courses or refresher training. Many accrediting bodies set renewal periods, such as every 3-5 years, to ensure trainers stay updated on the latest regulations and techniques. Renewal may also require demonstrating ongoing competence through assessments or practical evaluations. Keeping certifications current is essential for maintaining credibility and ensuring trainers provide up-to-date, compliant, and effective manual handling training in the workplace.
Effective manual handling training is crucial for workplace safety, reducing injuries, and fostering a culture of compliance. Continuous improvement ensures long-term benefits for both employees and organizations.
11.1 Summary of Key Points
Manual handling train-the-trainer programs emphasize proper techniques, legal compliance, and risk assessment to minimize workplace injuries. Trainers must ensure employees understand safe practices, legal responsibilities, and the importance of continuous improvement. Effective training fosters a culture of safety, reducing musculoskeletal disorders and enhancing overall workplace well-being. By equipping trainers with the necessary skills, organizations can ensure sustained compliance and a proactive approach to health and safety standards.
11.2 The Impact of Effective Training
Effective manual handling training significantly reduces workplace injuries and enhances employee confidence in performing tasks safely. It promotes a culture of safety, improving overall productivity and reducing absenteeism. Organizations benefit from lower injury-related costs and increased employee retention. Proper training also fosters a proactive approach to workplace health, ensuring compliance with legal standards and creating a sustainable, injury-free environment for all staff members.
11.3 Future Trends in Manual Handling Training
Future trends in manual handling training emphasize technology integration, such as e-learning modules and wearable devices for real-time feedback. Virtual and augmented reality are expected to enhance immersive training simulations, improving engagement and practical understanding. Personalized training programs, leveraging data analytics, will address specific risks and needs. Additionally, there is a growing focus on proactive health monitoring and holistic well-being strategies, aiming to create safer, healthier work environments.