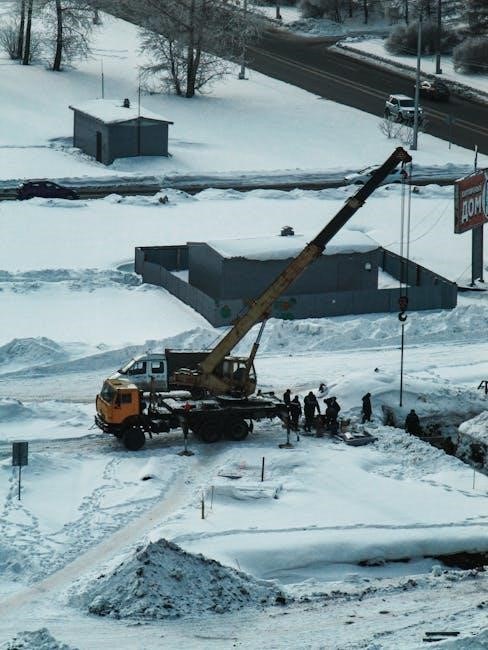
Manual cranes are essential tools in material handling, offering precise control for lifting and moving loads. They are versatile, cost-effective, and widely used in various industries.
1.1 Overview of Manual Cranes
Manual cranes are portable, versatile lifting devices used to move loads in various settings. They rely on human operation, often involving levers or wheels, to lift and position materials. These cranes are widely used in construction, manufacturing, and warehousing due to their simplicity and cost-effectiveness. Unlike motorized cranes, manual cranes do not require electricity, making them ideal for remote or low-capacity applications. Their compact design allows easy installation and minimal space requirements. Manual cranes are equipped with essential safety features, ensuring secure load handling and operator protection. They remain a reliable choice for efficient material handling in diverse industries.
1.2 Importance of Manual Cranes in Material Handling
Manual cranes play a crucial role in material handling by providing a cost-effective and efficient solution for lifting and moving loads. Their portability and ease of use make them ideal for small-scale operations or spaces with limited infrastructure. Unlike heavy machinery, manual cranes require minimal setup and can be operated by a single person, reducing labor costs. They are essential in industries where precise load placement is necessary, such as workshops, warehouses, and construction sites; By enhancing productivity and safety, manual cranes are a vital tool in modern material handling systems, ensuring smooth workflow and operational efficiency.
1.3 Brief History and Evolution of Manual Cranes
Manual cranes have a rich history dating back to ancient civilizations, where primitive pulley systems were used for lifting. The concept evolved during the Middle Ages with the introduction of wooden cranes for construction. The Industrial Revolution brought significant advancements, including the use of steel and improved mechanisms. In the 20th century, manual cranes became more refined, with focus on safety and efficiency. Today, they remain essential in various industries, offering a reliable, low-maintenance solution for material handling. Their evolution reflects technological progress and the need for adaptable, user-friendly lifting equipment.
Types of Manual Cranes
Manual cranes come in various designs, including overhead traveling cranes, ideal for warehouses, crawler cranes for heavy-duty projects, gantry cranes for outdoor settings, and jib cranes for precise, versatile lifting solutions.
2.1 Floor-Mounted Manual Cranes
Floor-mounted manual cranes are stationary systems installed directly on the floor, providing excellent stability for lifting and moving loads. They are ideal for heavy-duty applications due to their robust construction.
These cranes are commonly used in industrial settings where permanent lifting solutions are required. Their installation ensures minimal vibration and precise control, making them suitable for sensitive operations. With high load capacities, they are a reliable choice for demanding material handling tasks.
2.2 Wall-Mounted Manual Cranes
Wall-mounted manual cranes are versatile lifting solutions ideal for spaces with limited floor area. They are mounted directly to a wall or structural beam, providing efficient load handling. These cranes are commonly used in warehouses, workshops, and construction sites due to their compact design. They offer precise control and are suitable for lighter to medium-duty applications. Wall-mounted cranes are easy to install and maintain, making them a cost-effective option for businesses. Their space-saving design ensures optimal use of available area while providing reliable material handling capabilities.
2.3 Gantry Cranes
Gantry cranes are large, heavy-duty cranes with an overhead gantry framework, ideal for construction, shipyards, and heavy manufacturing. They are typically mounted on rails for stability and can be fixed or portable. Known for their versatility, gantry cranes are operated manually, relying on human control for precise load handling. Their robust construction allows them to manage substantial weights, making them essential in industries requiring heavy lifting. Proper training and adherence to safety protocols are crucial for safe operation, emphasizing the importance of operator manuals and regular maintenance to ensure reliability and efficiency in demanding environments.
2.4 Jib Cranes
Jib cranes are versatile lifting solutions, commonly used in industrial settings for precise load handling. They consist of a rotating boom mounted on a wall or floor, allowing for easy maneuverability. These cranes are ideal for applications requiring frequent adjustments and are often used in workshops, warehouses, and construction sites. Their compact design makes them suitable for limited spaces, while their durability ensures long-term reliability. Jib cranes are preferred for their flexibility and ability to handle a variety of loads efficiently, making them a valuable asset in material handling operations.
Components of Manual Cranes
Manual cranes consist of a hoist, trolley system, boom, control systems, and load monitoring devices, ensuring efficient and safe material handling operations.
3.1 Hoist and Its Mechanism
The hoist is a critical component of manual cranes, responsible for lifting and lowering loads. It operates using a pulley system with wire ropes or chains, powered by manual effort or small motors. The mechanism includes a gear system to reduce effort, ensuring smooth and controlled load movement. Proper lubrication and regular maintenance of the hoist are essential to prevent wear and ensure safety. Modern hoists often feature load-monitoring devices to prevent overloading, enhancing operational efficiency and reliability in various industrial settings.
3.2 Trolley System
The trolley system is a crucial component of manual cranes, enabling smooth movement of the hoist along the crane’s boom or bridge. It consists of wheels and a track system, allowing precise load positioning. Manual trolleys are operated by hand, while motorized options offer remote control for heavier loads. Proper maintenance, including lubrication and inspection, ensures optimal performance. The trolley’s design must align with the crane’s capacity and application, ensuring safe and efficient material handling. Regular checks are essential to prevent wear and tear, guaranteeing reliable operation and operator safety.
3.3 Boom and Its Construction
The boom is a critical component of manual cranes, designed to support and stabilize the load during lifting operations. Constructed from durable materials like steel or aluminum, it provides structural integrity and flexibility. The boom’s length and design vary depending on the crane type, with options for fixed or adjustable configurations. Proper construction ensures optimal load distribution, minimizing deflection under stress. Regular inspection and maintenance are essential to prevent wear and tear, ensuring safe and efficient operation. The boom’s robust build and precise engineering make it a cornerstone of manual crane functionality and reliability in material handling tasks.
3.4 Control Systems
Control systems in manual cranes are designed to ensure precise and safe operation. They typically include levers, pedals, or pushbutton pendants that regulate movement and load handling. These systems are often equipped with load monitoring devices to prevent overloading, enhancing safety. Emergency stop mechanisms are also integrated to halt operations immediately in case of hazards. Compliance with standards like OSHA and ASME ensures reliability and performance. Regular maintenance of control systems is crucial to maintain operational integrity and prevent malfunctions. Proper training for operators is essential to maximize efficiency and safety.
3.5 Load Monitoring and Safety Devices
Manual cranes are equipped with load monitoring systems to ensure safe operation. These devices include overload protection, emergency stops, and load-sensing technologies. They prevent accidents by alerting operators to potential overloads and ensuring stable lifting. Modern cranes may feature integrated weighing units that adapt to load conditions, enhancing precision and safety. Regular inspection of these devices is crucial to maintain reliability and compliance with safety standards, ensuring efficient and secure material handling in various industrial settings.
Safety Considerations and Precautions
Manual crane operation requires strict adherence to safety protocols, including proper load handling, use of PPE, and emergency preparedness to minimize risks and ensure safe working conditions.
4.1 Hazards Associated with Manual Crane Operation
Manual crane operation poses several hazards, including load instability, mechanical failures, and operator error. Overloading beyond capacity can cause structural damage or collapse. Improper rigging and sling angles may lead to load dropping. Environmental factors like uneven surfaces or poor lighting can increase risks. Additionally, operator fatigue or lack of training can result in accidents. Regular maintenance is crucial to prevent mechanical failures, while proper training ensures operators understand safe practices. Addressing these hazards is essential to safeguarding personnel and equipment, emphasizing the need for strict safety protocols and adherence to operational guidelines.
4.2 Risk Management Techniques
Risk management for manual crane operations involves systematic approaches to identify and mitigate hazards. Conducting thorough risk assessments ensures potential dangers are addressed; Load testing and regular inspections help prevent mechanical failures. Operators should be trained in proper techniques and safety protocols. Implementing safety devices, such as load limiters, enhances operational security. Emergency preparedness plans are crucial for quick response. Adhering to industry standards and manufacturer guidelines further reduces risks. By integrating these strategies, workplaces can minimize accidents and ensure safer crane operations, protecting both personnel and equipment from potential harm.
4.3 Personal Protective Equipment (PPE)
Personal Protective Equipment (PPE) is crucial for ensuring operator safety during manual crane operations. Hard hats protect against falling objects, while safety glasses guard eyes from debris. Gloves improve grip and prevent injuries from sharp edges. Steel-toe boots provide protection from heavy loads. High-visibility vests enhance worker visibility, reducing collision risks. In some cases, harnesses may be required to prevent falls. Proper use of PPE, combined with training, ensures compliance with safety regulations and minimizes workplace accidents. Always ensure PPE is well-maintained and worn correctly to maximize its protective benefits.
4.4 Load Handling and Stability
Proper load handling and stability are critical to safe manual crane operation. Always assess the load’s weight, shape, and balance before lifting. Use appropriate rigging equipment and ensure the load is securely attached. Avoid sudden movements, as they can destabilize the load. Maintain clear communication between operators and ground personnel to monitor the load’s position. Regular training on load dynamics and crane capacity helps prevent accidents. Ensure the crane is on a stable surface and follow manufacturer guidelines for load limits. Regular inspections of wire ropes, chains, and slings are essential for maintaining reliability.
- Always secure the load properly.
- Monitor the crane’s stability during operation.
- Train operators to handle unexpected shifts in load balance.
4.5 Emergency Preparedness
Emergency preparedness is vital for safe manual crane operation. Develop a comprehensive plan to address potential incidents like load drops or system malfunctions. Train operators and nearby personnel on evacuation procedures and first aid. Ensure clear communication protocols are in place for rapid response. Regular drills and simulations help prepare teams for real emergencies. Keep emergency contact information readily available and maintain a first aid kit on site. Compliance with OSHA and ASME standards ensures readiness for unforeseen situations. Proper documentation of incidents aids in improving future preparedness measures.
- Establish a clear emergency response plan.
- Conduct regular safety drills.
- Maintain communication devices and first aid supplies.
- Review and update emergency protocols annually.
Operating Principles and Techniques
Manual cranes rely on mechanical advantage and precise operator control. Techniques include proper load calculation, balanced lifting, and smooth movement to ensure efficiency and safety.
- Understand load weight and distribution.
- Use correct rigging and slinging methods.
- Maintain stability during operation.
5.1 Load Calculation and Capacity
Load calculation is critical for safe crane operation, ensuring the crane’s capacity is not exceeded. Factors like weight, dimensions, and center of gravity are assessed. Rated capacity must always be respected to prevent instability. Operators use manufacturer guidelines and load charts to verify limits. Proper rigging and sling angles also play a role in maintaining balance. Regular inspections ensure the crane remains within its capacity. Misjudging loads can lead to accidents, making accurate calculation essential for safety and efficiency. Always consult the crane’s manual for specific load limits and operating conditions to avoid overloading and potential failure.
5.2 Rigging and Slinging Techniques
Proper rigging and slinging are critical for safe and efficient crane operations. Operators must select appropriate slings based on load weight and type, ensuring correct sling angles to avoid damage. Regular inspection of slings for wear and tear is essential to prevent failures. Techniques include balancing loads, securing slings properly, and avoiding overloading. Training and adherence to safety guidelines are vital to minimize risks and ensure smooth lifting processes. Proper rigging practices also reduce the risk of accidents and extend equipment lifespan.
5.3 Understanding Sling Angles
Understanding sling angles is critical for safe and efficient manual crane operation. Proper sling angles ensure even load distribution, preventing imbalance and potential accidents. A wider angle increases stability, while a narrower angle can reduce lifting capacity. Operators must calculate optimal angles based on load weight and rigging setup. Incorrect angles can lead to load shifting or equipment damage. Regular training and experience help operators master this skill, ensuring safe and precise lifting practices in various industrial applications. Accurate angle management is essential for maintaining operational safety and efficiency. Always refer to manufacturer guidelines for specific sling angle recommendations.
5.4 Safe Lifting Practices
Safe lifting practices are paramount in manual crane operations to prevent accidents and ensure efficient load handling. Operators should always inspect rigging equipment before use, ensuring slings and components are free from damage. Load weight must not exceed the crane’s capacity, and proper tagging systems should be in place. Smooth, controlled movements are essential to avoid sudden jerks that might destabilize the load. Operators must maintain clear communication with ground personnel and ensure the area is clear of obstacles. Adhering to these practices minimizes risks and enhances workplace safety, making operations both efficient and secure.
5.5 Load Placement and Positioning
Proper load placement and positioning are critical for safe and efficient manual crane operation. Operators must ensure loads are centered and securely attached to prevent shifting during movement. Visual guides or laser indicators can aid in precise positioning. Loads should never overhang or extend beyond the crane’s capacity, as this can lead to instability. Smooth, controlled movements are essential to avoid sudden jerks that might cause accidents. Improper placement can result in load damage or equipment strain, emphasizing the need for careful planning and execution. Training and experience are key to mastering this skill.
Maintenance and Inspection
Regular lubrication of moving parts and thorough pre-operational inspections ensure safe operation. Replacing worn components promptly prevents mechanical failures and maintains efficiency in manual crane systems.
6.1 Routine Maintenance Requirements
Regular maintenance is crucial for manual cranes to ensure safe and efficient operation. Key tasks include inspecting wire ropes for wear, lubricating moving parts, and checking brakes and gears. Proper alignment of components is essential, and worn parts should be replaced promptly. Adhering to the manufacturer’s schedule and keeping maintenance records are vital. Additionally, visual inspections and cleaning of components help prevent issues. Proper upkeep minimizes downtime, enhances safety, and extends the crane’s lifespan, making it a critical part of facility management and ensuring optimal performance.
6.2 Pre-Operational Inspection Checklist
A pre-operational inspection is crucial for ensuring manual crane safety and efficiency. Start by checking all mechanical components, such as wire ropes, chains, and hooks, for wear or damage. Verify that safety devices, including load limits and emergency stops, are functioning properly. Lubricate moving parts as needed and ensure the trolley and hoist systems operate smoothly. Review the load chart to confirm the crane’s capacity for the intended task. Always refer to the manufacturer’s manual for specific guidelines. Conducting these checks helps prevent accidents and ensures reliable performance. Regular inspections are key to maintaining crane longevity and compliance with safety standards.
6.3 Lubrication of Moving Parts
Lubrication is vital for maintaining the functionality of manual cranes. Regularly apply high-quality grease to moving components like gears, bearings, and pivot points to reduce friction and prevent overheating. Inspect lubrication levels daily or before extended use, ensuring all parts are properly coated. Use the type of grease recommended by the manufacturer to avoid compatibility issues. Proper lubrication extends equipment life, reduces wear, and ensures smooth operation. Neglecting this step can lead to premature component failure and safety hazards. Always follow the maintenance schedule outlined in the crane’s manual for optimal performance and longevity.
6.4 Replacement of Worn Components
Regular inspection identifies worn components, such as wire ropes or hoist brakes, which must be replaced promptly. Timely replacement prevents equipment failure and ensures safety. Always follow manufacturer guidelines for part replacement and maintain records of maintenance activities. Delaying replacements can lead to costly repairs or accidents. Proper installation of new components is critical to maintain crane efficiency and reliability. Using genuine or approved spare parts ensures compliance with safety standards and extends the crane’s operational life.
Applications of Manual Cranes
Manual cranes are widely used in industrial settings, construction sites, and warehousing for efficient material handling, ensuring reliability and precision in lifting and moving loads safely.
7.1 Industrial and Manufacturing Settings
Manual cranes play a crucial role in industrial and manufacturing environments, offering precise load handling for assembly lines, machine shops, and warehouses. Their compact design and ease of installation make them ideal for facilities with limited space. Often used for lifting heavy machinery parts, tools, and raw materials, manual cranes enhance workflow efficiency and reduce manual labor. With customizable load capacities and ergonomic designs, they adapt to diverse production needs, ensuring safe and reliable material movement. Regular maintenance and operator training are essential to optimize their performance in demanding industrial settings.
7.2 Construction Sites
Manual cranes are widely used on construction sites for lifting and moving materials, such as bricks, concrete blocks, and steel beams. Their portability and ease of operation make them ideal for smaller-scale tasks or locations with limited space. These cranes are often employed in areas where heavy machinery cannot reach, ensuring efficient workflow and safety. They are particularly useful for precise placement of loads, reducing the risk of accidents and improving overall site productivity.
Their compact design allows manual cranes to operate in tight spaces, making them indispensable for construction projects. Proper training and adherence to safety guidelines are essential for operators to handle these cranes effectively, ensuring smooth operations and minimizing hazards on the site.
7.3 Warehousing and Logistics
Manual cranes play a vital role in warehousing and logistics by efficiently handling materials within confined spaces. They are ideal for lifting and moving goods, ensuring smooth workflow and minimizing storage constraints. With their precision and control, manual cranes are often used for loading and unloading goods, as well as arranging inventory. Their compact design and ease of operation make them a cost-effective solution for managing smaller-scale lifting tasks. Additionally, they enhance safety by reducing manual handling risks and ensuring proper load placement, making them indispensable in modern logistics operations.
Their reliability and versatility contribute significantly to optimizing warehouse operations, ensuring timely and secure material handling.
Regulations and Standards
Manual cranes must comply with industry standards and regulations to ensure safety and efficiency. Adherence to these guidelines is crucial for proper operation and legal compliance.
8.1 OSHA Guidelines for Crane Operation
OSHA guidelines for crane operation emphasize operator training, equipment inspection, and safe load handling. Operators must be certified and trained to manage risks effectively. Regular inspections are mandatory to ensure crane components function properly. Load testing and proper rigging practices are critical to prevent accidents. Employers must maintain operational manuals and ensure compliance with safety standards. Emergency procedures, such as load control during power failures, must be established. Adherence to these guidelines minimizes hazards and ensures a safe working environment for all personnel involved in crane operations.
8.2 ASME Standards for Crane Safety
ASME standards provide comprehensive guidelines for ensuring the safety and reliability of cranes. These standards cover design, manufacturing, testing, and maintenance practices. They specify requirements for load capacity, structural integrity, and operational safety. Regular inspections and maintenance are mandated to prevent failures. Compliance with ASME standards helps minimize risks and ensures safe crane operation. These standards are widely adopted across industries to protect workers and equipment. By adhering to ASME guidelines, organizations can maintain a safe working environment and prevent potential accidents.
8.3 Compliance with Local Regulations
Compliance with local regulations is critical when operating manual cranes. Adherence to regional building codes, safety standards, and environmental laws ensures legal and safe operations. Many jurisdictions require permits and regular inspections to validate crane safety. Non-compliance can result in fines, operational shutdowns, or legal penalties. Operators must stay informed about local ordinances and integrate them into their operational protocols. This includes adhering to specific load limits, noise restrictions, and zoning laws. Proper documentation and certification are often mandatory to demonstrate regulatory alignment. Always consult local authorities to ensure full compliance and avoid potential liabilities or disruptions.
Troubleshooting Common Issues
Identify mechanical failures, resolve load imbalances, and address control system malfunctions promptly to ensure smooth manual crane operations and prevent downtime.
9.1 Identifying Mechanical Failures
Identifying mechanical failures in manual cranes requires regular inspections and monitoring. Look for wear and tear on components like hoists, trolleys, and wire ropes. Check for unusual noises, excessive friction, or visible damage. Ensure all moving parts are properly lubricated to prevent overheating. Operators should report any irregularities immediately. Routine maintenance checks can help detect potential issues early. Keeping a maintenance log ensures transparency and accountability. Early identification of mechanical failures prevents accidents and extends the crane’s lifespan. Always refer to the manufacturer’s guidelines for specific inspection procedures.
9.2 Resolving Load Imbalance Issues
Load imbalance in manual cranes can lead to instability and accidents. To address this, operators should first identify uneven weight distribution by observing the crane’s behavior. Adjusting the rigging or redistributing the load can help restore balance. Ensuring proper sling angles and verifying load calculations are critical. If issues persist, inspecting the crane’s mechanical components for misalignment or wear is essential. Regular maintenance and operator training can prevent such problems, ensuring smooth and safe operations. Always refer to the manufacturer’s guidelines for specific troubleshooting steps.
9.3 Addressing Control System Malfunctions
Control system malfunctions in manual cranes can disrupt operations and pose safety risks. Common issues include faulty sensors, wiring problems, or software glitches. Operators should first consult the vendor manual for troubleshooting guidance. Conducting a thorough diagnostic check, reviewing error logs, and resetting systems often resolve minor issues. In severe cases, replacing damaged components or recalibrating the system may be necessary. Regular inspections and preventive maintenance can help mitigate such malfunctions. Ensuring proper training and adherence to safety protocols is crucial for maintaining reliable control system performance.
- Consult vendor manuals for troubleshooting steps.
- Perform diagnostic checks and review error logs.
- Reset or recalibrate systems as needed.
- Replace faulty components promptly.
- Implement preventive maintenance routines.
Manual cranes are versatile, efficient tools for material handling. Proper operation, maintenance, and adherence to safety protocols ensure reliability. Future advancements promise enhanced performance and safety.
10.1 Summary of Key Points
Manual cranes are versatile and cost-effective tools for material handling, offering precise control over loads. They are available in types like floor-mounted, wall-mounted, gantry, and jib cranes, each suited for specific applications. Essential components include hoists, trolleys, booms, and control systems, ensuring efficient operation; Safety is paramount, with measures like load monitoring, PPE, and regular inspections. Proper training, adherence to regulations, and routine maintenance are critical for optimal performance and longevity. Their applications span industries like manufacturing, construction, and logistics, making them indispensable in modern workflows.
10.2 Future Trends in Manual Crane Technology
Future trends in manual crane technology include integration with Industry 4.0, automation, and IoT for real-time monitoring. Advances in materials science will lead to lighter, stronger components. Energy-efficient designs and eco-friendly power sources are expected to rise. Smart cranes with AI for predictive maintenance and load optimization will become common. Enhanced safety features, such as collision detection and automated overload protection, will improve operational reliability. These innovations aim to increase productivity while reducing environmental impact and ensuring safer workplaces across industries.